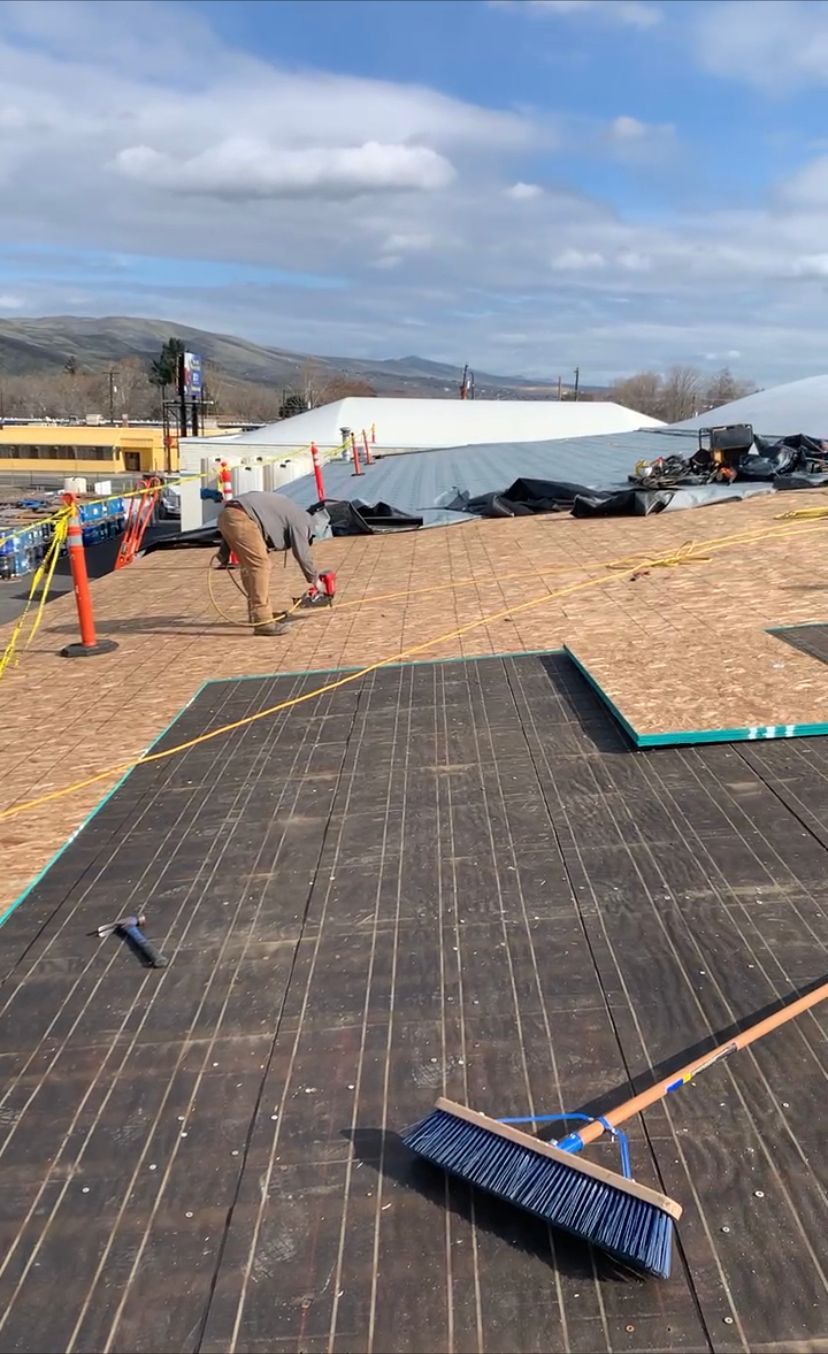
Solutions that make sense!
Low Slope Products
GAF TPO
GAF PVC
PolyGlass ElastoFlex
Nu-Ray Metals Standing Seam
Built Up Roofs
Maintenance Programs
Aluminum Coating Applications
Restraunt Grease Cleaning
Restaurants
Restaurant Solutions
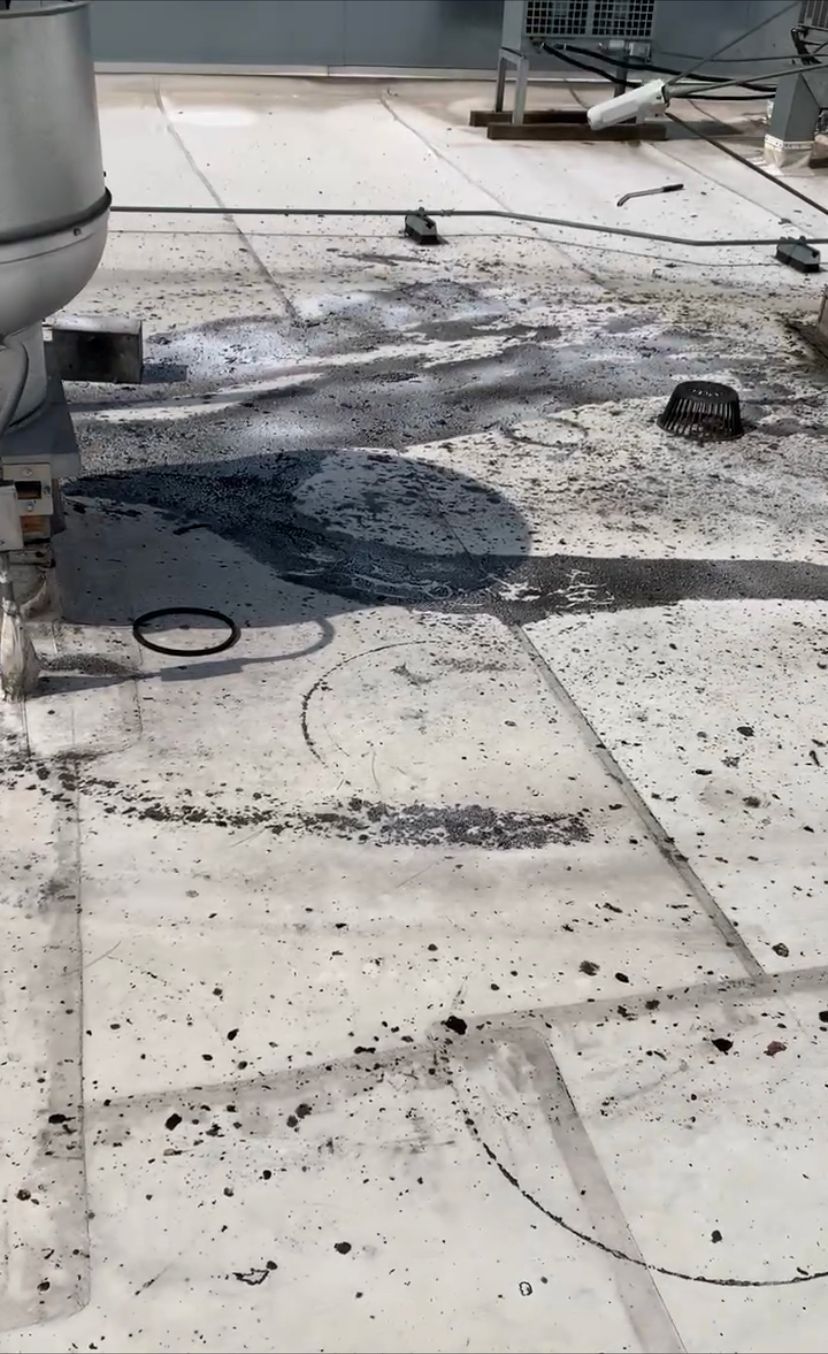
The Problem
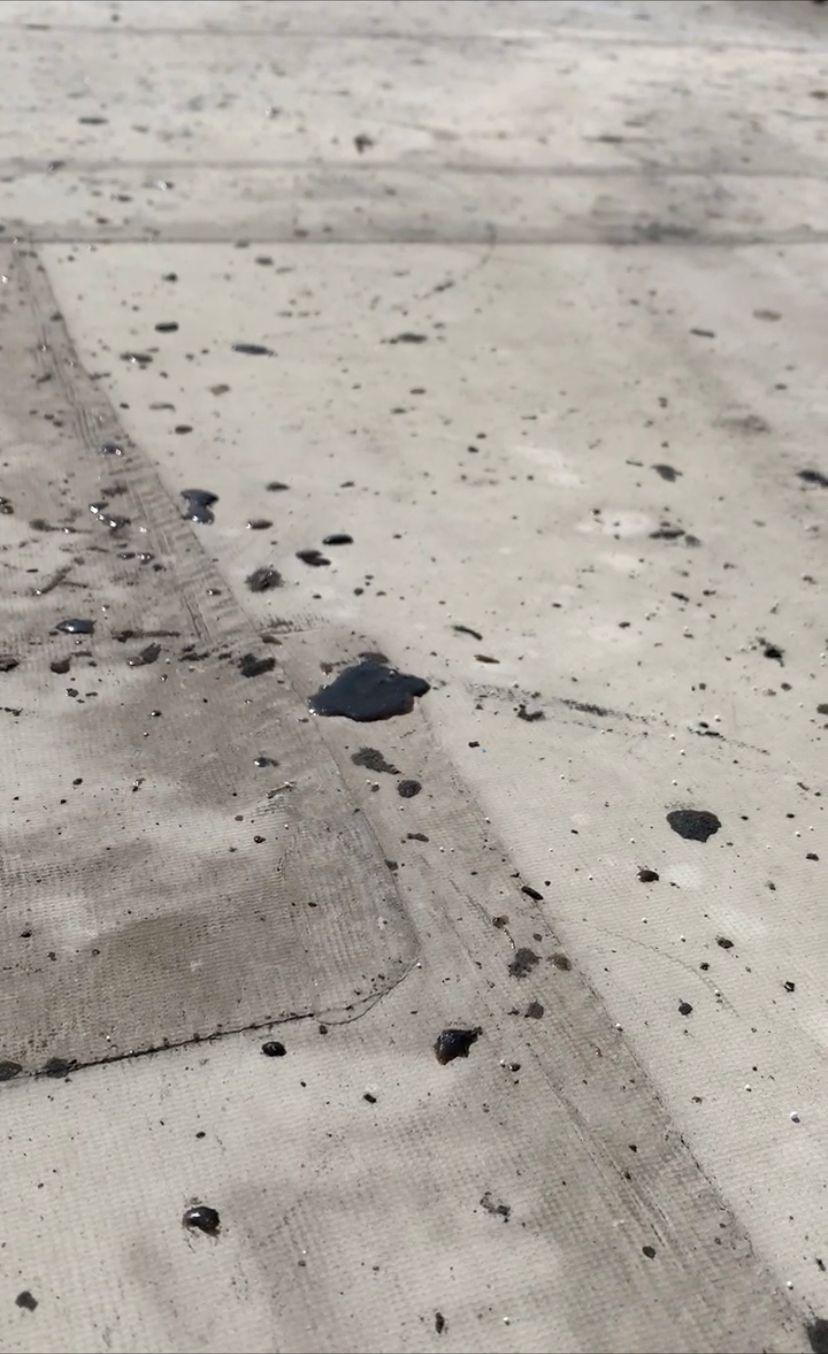
Hood Vent's are designed to remove moisture and grease from the kitchen and expel it through a series of duct work that lead to the roof hood vent. The grease must be cleaned routinely in the kitchen and all ducting. The hood vent's grease traps must also be emptied on a regular basis.
Grease traps are not always emptied on a regular basis or often enough and rivers of grease flow across the roof until they drain into the roof drains. Grease can wreck havoc on the sewer system but worse the fasts and oils can find it's way to a stream or river and has the potential to kill wildlife.
Once the grease has landed on the roof it will harden and slowly eat away at your roof. Even PVC roofs that are chemically resilient will suffer over time.
The Solution
Yakima Roofing & Remodeling, LLC has several cleaning plans tailored for to your needs. Let help keep your roof grease free and your business compliant with Washington State Regulations.
Cleaning grease should be done by a professional who has:
- Proper training mixing and applying caustic products
- Has proper Personal Protect equipment
- Under stands the risks and safety protocols in case of spills or accidents
- Has Safety training & First Aide Training
We offer three cleaning plans to suit your needs. Plan A is for hood vent's that are regularly cleaned and the roof see's minimal spills. Our Plan B is for roofs that need quarterly cleanings due to more frequent spills and our Plan C is tailored for monthly cleanings. If you need help choosing a plan give us a call and we will evaluate your roof's needs.
Low Slope Roof Systems
Systems
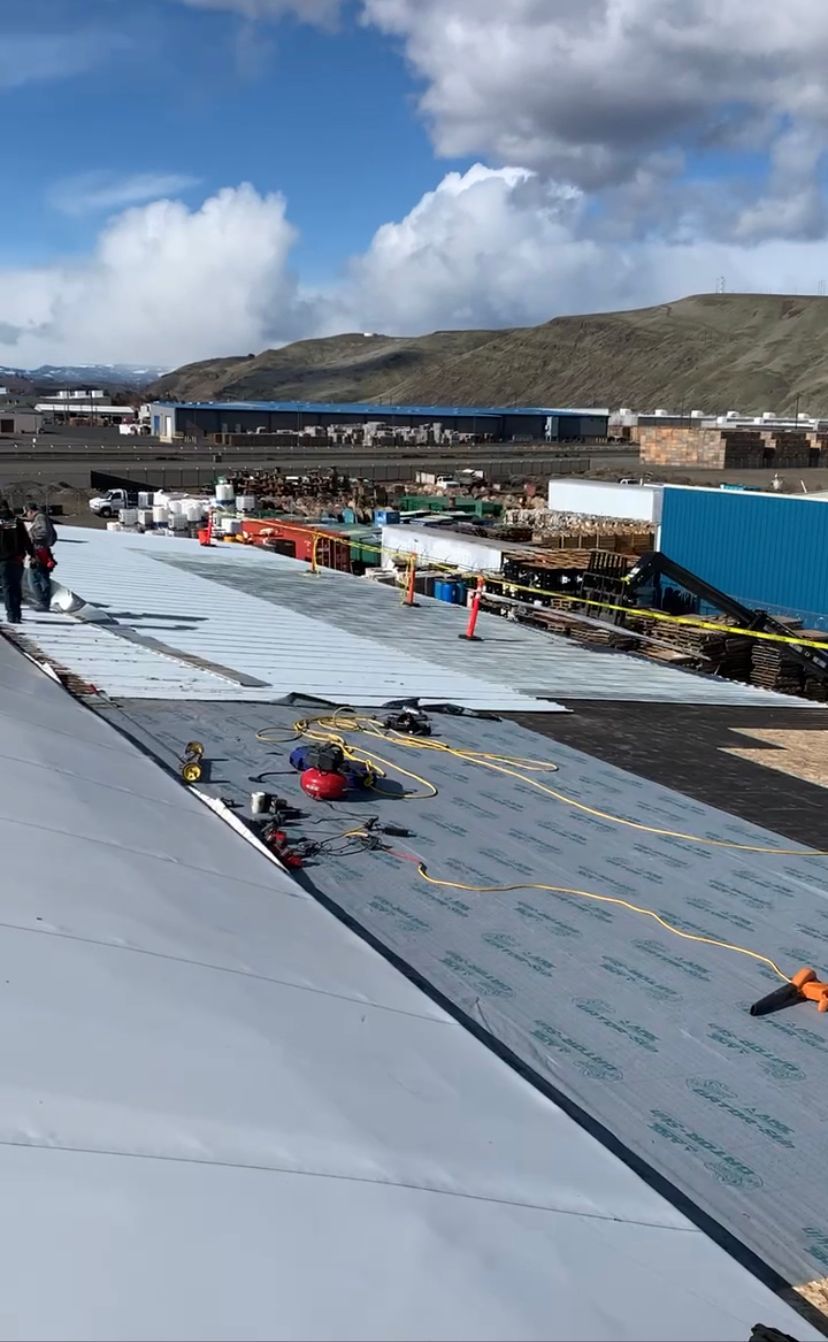
The Problems
Low-slope roof systems are not just for commercial buildings. Most homes have sloped roof pitches greater than 3:12 and require a sloped roof system.
However, some homes may have sections that are considered low slope, less than 3:12 pitch, and require different waterproofing methods. Patio covers and carports may also have low slope pitches.
Low-slope roof sections do not drain away moisture as efficiently as sloped roofs do. Pooling is a common issue where the moisture can spread in all directions. Because of this issue, the system must be monolithic to prevent leaks.
A sloped roof system is not monolithic, this means it must be installed on a slope, or water may travel under the shingles, rust out nails, and infiltrate the system causing leaks.
The Solutions
TPO & PVC is a great choice when you have a large roof area to cover. If installed correctly it can be a maintenance-free system, unlike the older built-up roof systems.
The other benefit to TPO & PVC alike is that the flashings are made of the same materials and will last the life of the roof. With built-up roof systems pipes are flashed with lead flashings and lots of mastic and glass reinforcements that don't typically hold up for the life of the roof.
Patching over punctures caused by other trades working on the roof is also easy and will last the life of the roof.
Elasto-Flex peal and stick systems are a good choice for patio covers, carports, or small flat areas that are visible on your roof. They are granulated and come in a variety of colors to match the surrounding shingles.
Standing Seam if Metal is desired on a low slope around 2:12 pitch a standing seam metal with a factory seal is the way to go. The factory seal acts as a gasket after the standing seam is folded over the next panel and crimped either by hand or a seamer.
Maintenance Solutions
Built-up roof system
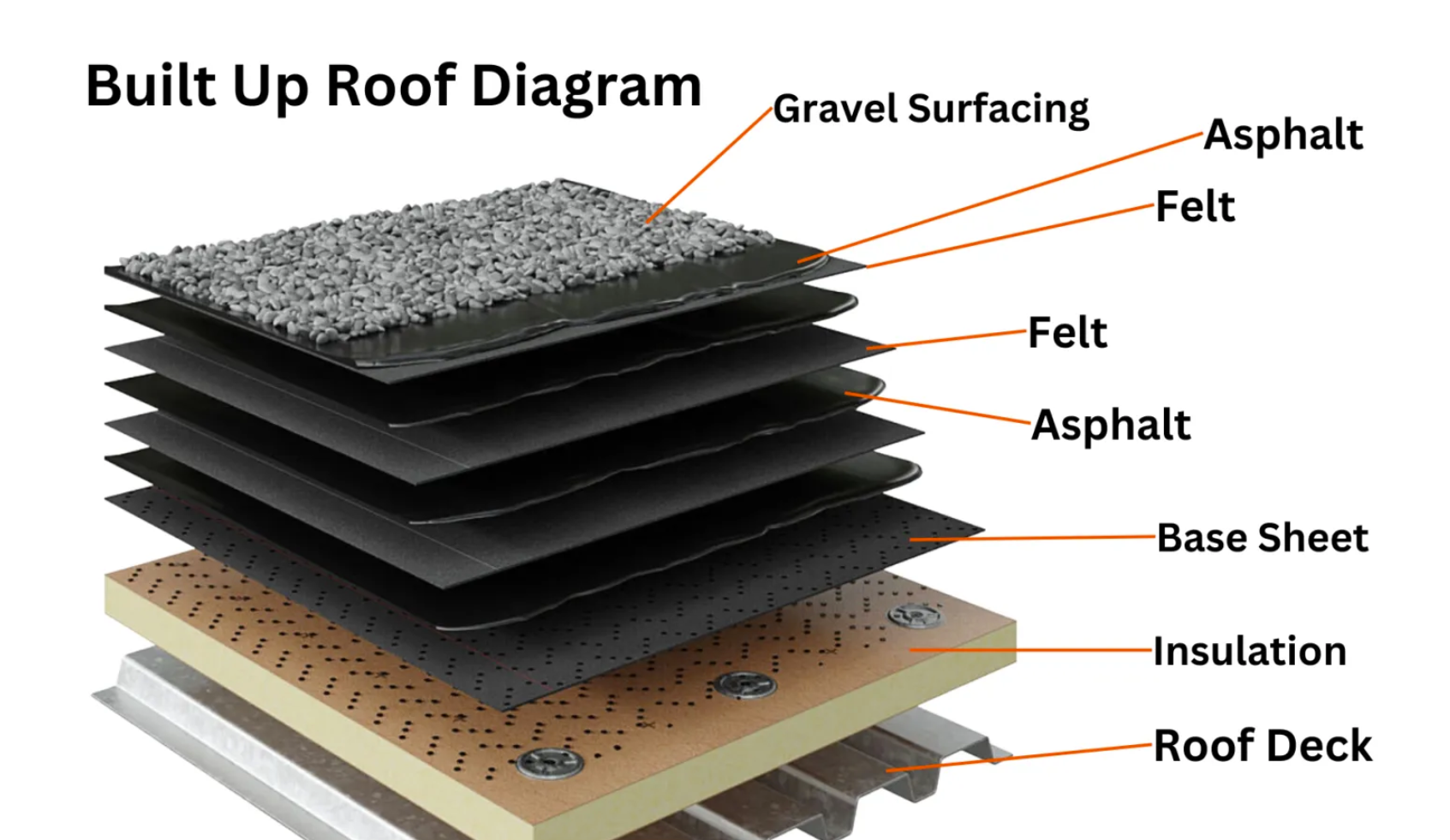
The Problems
Built-up roof systems are nearly a system of the past due to higher insurance rates that forced many contractors to abandon their hot tar kettles for heat guns, Thermoplastic Polyolefin, PVC, and EPDM systems.
Now with many built-up roof systems on the brink of failure most new roofing contractors never had the experience of installing a built-up roof the knowledge of how to maintain them is nearly lost.
Built-up roof systems may often have more life but can't limp across the finish line due to flashing failures and buckling that causes cracks and failure. When the roof begins to buckle or the flashings begin to fail it's typically time for a new roof.
In some cases, the roof itself may still have a few years of life remaining but most roofing contractors haven't worked with built-up roof systems and do not understand the proper methods to maintain them.
The Solution
An evaluation must be done to determine if a BUR roof system can or should be maintained or if it's time for a new roof. If the system is still relatively flat with only one or two large buckles then we can most likely put the roof on a maintenance plan.
Even when the BUR is in very bad shape it's still possible to maintain it for a short time to help the building owner buy time to get finances in place for a new roof.
When a BUR roof needs late-life maintenance the sole purpose is to buy the property owner time to plan financially for a new roof. Yakima Roofing & Remodeling, LLC will help you with this goal by providing an estimated cost with future price increases and a maintenance plan to help you stay leak-free while finances come together.
Our recommendations are to give yourself time and call today for a free evaluation to determine the remaining life of your roof. With proper planning, you can plan your budget with ease and at the same time help your BUR cross the finish line without all the harmful leaks.
Common Q&A
Ready to start your next commercial roofing project? Call 509-907-7206 for a quote.